Drill Attachment for Brushing out Slide
-
- Posts: 0
- Joined: Sat Mar 31, 2018 11:58 am
Drill Attachment for Brushing out Slide
Yup. You read that correctly. I'm imagining a type of cleaning rod I can torque down into my drill that would be a standard cleaning rod, but with a few key differences:
1. A hex-type profile at the top to allow it to interface into a hand drill
2. Several soft brushes along the length of the rod
I think this would be really nice, and convenient for a responsible adult to thoroughly clean the slide. The many brushes along the rod's length would help keep the metal of the rod out of contact with the slide itself. Nothing like a flex-hone...much softer.
Good idea?
1. A hex-type profile at the top to allow it to interface into a hand drill
2. Several soft brushes along the length of the rod
I think this would be really nice, and convenient for a responsible adult to thoroughly clean the slide. The many brushes along the rod's length would help keep the metal of the rod out of contact with the slide itself. Nothing like a flex-hone...much softer.
Good idea?
-
- Posts: 0
- Joined: Sat Mar 31, 2018 12:15 pm
Drill Attachment for Brushing out Slide
You might want to look at brushes for cleaning out heat exchanger tubes.
I'd suggest a Bore Mop. It's a soft attachment that goes on a gun cleaning rod. One that fits a 28 Gauge shotgun is about the diameter of a slide tube and is about 3 inches long. I've seen solid rods that accept the bore mop, although most gun cleaning kits have sectional rods (you can probably glue them together if you don't want to ever take them apart).
It doesn't have a hex end; you'll need a chuck to grab it. I have a chuck that has a hex base that came with one drill. I'm sure you can find one pretty easily.
Here's a picture of a bore mop:
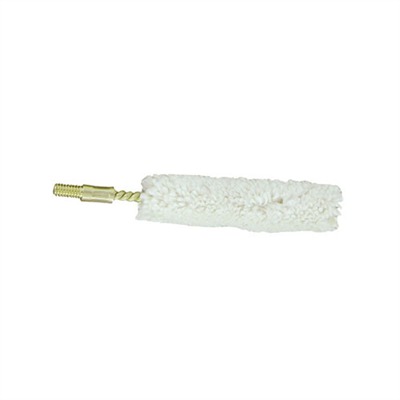
I'd suggest a Bore Mop. It's a soft attachment that goes on a gun cleaning rod. One that fits a 28 Gauge shotgun is about the diameter of a slide tube and is about 3 inches long. I've seen solid rods that accept the bore mop, although most gun cleaning kits have sectional rods (you can probably glue them together if you don't want to ever take them apart).
It doesn't have a hex end; you'll need a chuck to grab it. I have a chuck that has a hex base that came with one drill. I'm sure you can find one pretty easily.
Here's a picture of a bore mop:
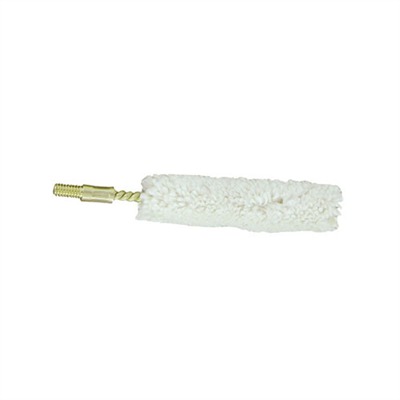
-
- Posts: 0
- Joined: Sat Mar 31, 2018 11:57 am
Drill Attachment for Brushing out Slide
I have thought about the very same idea... I'll be interested to watch this thread...
-
- Posts: 0
- Joined: Sat Mar 31, 2018 11:59 am
Drill Attachment for Brushing out Slide
I already did that...
-
- Posts: 0
- Joined: Sat Mar 31, 2018 12:33 pm
Drill Attachment for Brushing out Slide
Quote from: Doug Elliott on Yesterday at 07:48 PMI already did that...
How did it work? I've been wanting to do this too. Or was it a fiasco?
How did it work? I've been wanting to do this too. Or was it a fiasco?
-
- Posts: 0
- Joined: Sat Mar 31, 2018 12:00 pm
Drill Attachment for Brushing out Slide
I took a snake that has the plastic-coated body with brushes on each end. I cut off one end, and now it will fit in the drill.
If you use one of these, you should keep your free hand cupped around the entrance to the outer slide tube that you are cleaning. If the drill speed gets too fast, the long plastic coated part can start swinging out, making the shape of a bow. Your hand cupped around it is enough to keep it from going out of control and potentially causing minor damage to your slide.
I only use this tool when I do a major cleaning to my slide - I like to use it to polish the inside of my outer slides with some Wrights brass Polish, after first cleaning everything with more traditional materials. After this treatment, the slide action is the best I've ever experienced.
Jim Scott
If you use one of these, you should keep your free hand cupped around the entrance to the outer slide tube that you are cleaning. If the drill speed gets too fast, the long plastic coated part can start swinging out, making the shape of a bow. Your hand cupped around it is enough to keep it from going out of control and potentially causing minor damage to your slide.
I only use this tool when I do a major cleaning to my slide - I like to use it to polish the inside of my outer slides with some Wrights brass Polish, after first cleaning everything with more traditional materials. After this treatment, the slide action is the best I've ever experienced.
Jim Scott
-
- Posts: 0
- Joined: Sat Mar 31, 2018 11:59 am
Drill Attachment for Brushing out Slide
You really need a lathe to make what I made for myself. I used a 3/8" aluminum rod and drilled/bored a hole in one end to press-fit a 1/4" hex Phillips bit into it so it would fit in a cordless screwdriver. The hole needs to be absolutely straight, that's the reason for the lathe. You could tap the other end for a bore mop as Bruce suggested. I formed a slot like a standard cleaning rod has. And rounded the end, and marked on the rod where the maximum insertion should be to avoid going into the end bow.
It would be very easy to cause significant damage to a slide or even hurt yourself with that setup - I'm not recommending it, only telling what I did. I use it only to clean a slide that has been sitting a long time unused.
It would be very easy to cause significant damage to a slide or even hurt yourself with that setup - I'm not recommending it, only telling what I did. I use it only to clean a slide that has been sitting a long time unused.
-
- Posts: 0
- Joined: Sat Mar 31, 2018 11:53 am
Drill Attachment for Brushing out Slide
Doug,
To me it looked like a key aspect of the original post was "several soft brushes along the length." Certainly the part that caught my attention.
Having soft spacers along the rod makes the idea different from the others noted here so far. I would imagine those to be something like the bore mop Bruce showed, but with threading at BOTH ends.
Even with those, having the "drive" concentric would be important. Most home drills have enough torque to whip things sideways given even a little off-center twist!
I suppose the spacers COULD be foam. But that would require some sort of retaining system... and if the retainers whipped around inside the outer slide... too ugly to think about.
So, some sort of bore mop... but it would have to be made from scratch the way the one Bruce showed is (fiber fed through wires that will then be twisted and crimped into a threaded connector... two in this case.)
Maybe a gun forum would provide more options?
To me it looked like a key aspect of the original post was "several soft brushes along the length." Certainly the part that caught my attention.
Having soft spacers along the rod makes the idea different from the others noted here so far. I would imagine those to be something like the bore mop Bruce showed, but with threading at BOTH ends.
Even with those, having the "drive" concentric would be important. Most home drills have enough torque to whip things sideways given even a little off-center twist!
I suppose the spacers COULD be foam. But that would require some sort of retaining system... and if the retainers whipped around inside the outer slide... too ugly to think about.
So, some sort of bore mop... but it would have to be made from scratch the way the one Bruce showed is (fiber fed through wires that will then be twisted and crimped into a threaded connector... two in this case.)
Maybe a gun forum would provide more options?
-
- Posts: 0
- Joined: Sat Mar 31, 2018 11:58 am
Drill Attachment for Brushing out Slide
I wouldn't use a drill. I'd use something really soft attached to a Dremel with low torque but high RPM. I believe Otis makes a long flexible bore snake and you'd just need to attach a really soft end brush/mop.
-
- Posts: 0
- Joined: Sat Mar 31, 2018 11:59 am
Drill Attachment for Brushing out Slide
There are probably two distinct ways this device could go:
1) Make a motorized brushing unit for cleaning
2) Make a motorized burnishing unit for polishing.
I don't see any advantage to a motorized brushing unit vs using a hand snake for routine cleaning. However, perhaps it could be useful for cleaning an old horn that has set for an extended period of time. In that case, wouldn't burnishing after hand-cleaning still be called for?
One danger to the horn in using a motorized burnishing unit could be some loss of metal if the device is used too often and too aggressively - same as using Brasso.
In either case, I don't think anything would clean out a slide full of mineral deposits better than a chemical flush to begin with, followed by a burnishing.
Where are the techs?
...Geezer
1) Make a motorized brushing unit for cleaning
2) Make a motorized burnishing unit for polishing.
I don't see any advantage to a motorized brushing unit vs using a hand snake for routine cleaning. However, perhaps it could be useful for cleaning an old horn that has set for an extended period of time. In that case, wouldn't burnishing after hand-cleaning still be called for?
One danger to the horn in using a motorized burnishing unit could be some loss of metal if the device is used too often and too aggressively - same as using Brasso.
In either case, I don't think anything would clean out a slide full of mineral deposits better than a chemical flush to begin with, followed by a burnishing.
Where are the techs?
...Geezer
-
- Posts: 0
- Joined: Sat Mar 31, 2018 12:00 pm
Drill Attachment for Brushing out Slide
Don't see why you couldn't just use a gun cleaning kit. cut the handle off and you have a long aluminum pole to put in drill and can screw in replaceable soft cotton swabs tips or plastic brush tips. 28ga shotgun brushes/swabs should work fine. You'd just have to be careful not to let any of the metal parts touch the sides/bow. checkout brownell's for supply if you can't find them locally.
-
- Posts: 0
- Joined: Sat Mar 31, 2018 12:15 pm
Drill Attachment for Brushing out Slide
I did a little research on the heat exchanger brush idea.
Most heat exchangers are made from tubes that make a trombone look puny. But even for a 20 foot heat exchanger they use a "short" (6 inch) brush on a long flexible shaft. The shafts are turned by things that make a home drill look puny. The shafts are not bare steel; they are coated. Often heat exchanger tubes are brass and the problems with damage are the same.
I might recommend a different tack. Maybe a VERY slow drill speed so you don't get the whipping action on the shaft. I have a drill-driver that can turn pretty slowly (you don't want to screw in a bolt at 1700 RPM -- easy way to lose a head).
Most heat exchangers are made from tubes that make a trombone look puny. But even for a 20 foot heat exchanger they use a "short" (6 inch) brush on a long flexible shaft. The shafts are turned by things that make a home drill look puny. The shafts are not bare steel; they are coated. Often heat exchanger tubes are brass and the problems with damage are the same.
I might recommend a different tack. Maybe a VERY slow drill speed so you don't get the whipping action on the shaft. I have a drill-driver that can turn pretty slowly (you don't want to screw in a bolt at 1700 RPM -- easy way to lose a head).
-
- Posts: 0
- Joined: Sat Mar 31, 2018 11:57 am
Drill Attachment for Brushing out Slide
I'm picturing a shaft like Doug made, supported by two bearings at one end. A long cord is wrapped around the shaft between the two bearings and attached to a weight (so the bearings need to be close enough the shaft doesn't bow.
Drop the weight, the rod spins as the cord unwinds, you gently insert the side over the rod as the brush on the end of the rod spins. No power needed, no chance of it getting away from you. Do it by candle light during a power outage.
For most of us if we use a regular cleaning rod often enough we should never have a slide that needs this kind of aggressive approach. But I can see a neglected slide or ebay purchase benefiting.
Something i learned just this summer: pBone slides can be pretty good IF you swab them dry after every use and keep them coated with automotive wax. Those brass stockings corrode instantly if you don't and then they drag. Wish I'd known that when I first got one.
Drop the weight, the rod spins as the cord unwinds, you gently insert the side over the rod as the brush on the end of the rod spins. No power needed, no chance of it getting away from you. Do it by candle light during a power outage.
For most of us if we use a regular cleaning rod often enough we should never have a slide that needs this kind of aggressive approach. But I can see a neglected slide or ebay purchase benefiting.
Something i learned just this summer: pBone slides can be pretty good IF you swab them dry after every use and keep them coated with automotive wax. Those brass stockings corrode instantly if you don't and then they drag. Wish I'd known that when I first got one.
-
- Posts: 0
- Joined: Sat Mar 31, 2018 11:59 am
Drill Attachment for Brushing out Slide
I'm really not sure why there should be any concern about a smooth metal rod perhaps contacting the inside of the slide tube... Isn't that what's happening when you play?
Low speed is the way to go. Even a little friction builds up a lot of heat quickly at high speed.
Low speed is the way to go. Even a little friction builds up a lot of heat quickly at high speed.
-
- Posts: 0
- Joined: Sat Mar 31, 2018 11:58 am
Drill Attachment for Brushing out Slide
The fellow who recently smoothed out a couple of dents in my bell stem told me about a bench-mounted motor he uses for slide tube treatment, with a pedal to control the speed.
-
- Posts: 0
- Joined: Sat Mar 31, 2018 12:34 pm
Drill Attachment for Brushing out Slide
Even for me, except for a slide in very bad shape, this is just way overkill to accomplish a very simple job......
R. Goldberg
R. Goldberg
-
- Posts: 0
- Joined: Sat Mar 31, 2018 11:53 am
Drill Attachment for Brushing out Slide
I am still surprised by the number of DIY folks willing to risk handslides, tuning slides, leadpipes, mouthpieces, etc., to test an idea. I found out long ago through personal experience that using home-made tools or anything other than what's recommended or available over the counter is rarely a good idea. If I can't clean my slide with mild soap and water, a vinyl-coated snake, and a cleaning rod with cheesecloth (or muslin), then I leave it to a tech. For everyday maintenance, a Brass Saver is a nice inexpensive swab.
-
- Posts: 0
- Joined: Sat Mar 31, 2018 11:53 am
Drill Attachment for Brushing out Slide
The main reason why I find this interesting is that it could put the dominant buffing direction at right angles to what we have now with regular cleaning. Overhauling an air rifle got me thinking about it. On air rifles it is essential to maintain a very good seal between the piston and cylinder. Part of that involves NOT polishing the cylinder, but cross-hatching it, so it will hold lube better.
Trombone slides won't work with the kind of seal on an air rifle. But they DO need to retain lube. If Sliphorn comes up with something that can do a reasonable job of cross-hatching with very fine abrasive (like Wright's water soluable polish) I'd certainly be game to try it.
Trombone slides won't work with the kind of seal on an air rifle. But they DO need to retain lube. If Sliphorn comes up with something that can do a reasonable job of cross-hatching with very fine abrasive (like Wright's water soluable polish) I'd certainly be game to try it.
-
- Posts: 0
- Joined: Sat Mar 31, 2018 11:58 am
Drill Attachment for Brushing out Slide
I haven't even seen an air rifle for at least 40 years, but IIRC the bore is steel and the piston has a leather, or perhaps nowadays, neoprene or similar bucket.
I agree that you would benefit from a very light crosshatch to help the steel retain lube reliably. Brass, on the other hand, is relatively porous compared to steel. This makes me think that deliberately introducing a cross hatch might actually be detrimental.
Just theorising here...
I agree that you would benefit from a very light crosshatch to help the steel retain lube reliably. Brass, on the other hand, is relatively porous compared to steel. This makes me think that deliberately introducing a cross hatch might actually be detrimental.
Just theorising here...
-
- Posts: 0
- Joined: Sat Mar 31, 2018 11:53 am
Drill Attachment for Brushing out Slide
Quote from: Lawrie on Jul 01, 2017, 03:19PMI haven't even seen an air rifle for at least 40 years, but IIRC the bore is steel and the piston has a leather, or perhaps nowadays, neoprene or similar bucket.
I agree that you would benefit from a very light crosshatch to help the steel retain lube reliably. Brass, on the other hand, is relatively porous compared to steel. This makes me think that deliberately introducing a cross hatch might actually be detrimental.
Just theorising here...
Seems like good theory to me. On the one hand, the depth of hatching done with Wright's should be slight... on the other, this is NOT a new idea, so it is very unlikely Conn and others did not try it a hundred years ago.
Still, can't help but be curious
I agree that you would benefit from a very light crosshatch to help the steel retain lube reliably. Brass, on the other hand, is relatively porous compared to steel. This makes me think that deliberately introducing a cross hatch might actually be detrimental.
Just theorising here...
Seems like good theory to me. On the one hand, the depth of hatching done with Wright's should be slight... on the other, this is NOT a new idea, so it is very unlikely Conn and others did not try it a hundred years ago.
Still, can't help but be curious

-
- Posts: 0
- Joined: Sat Mar 31, 2018 11:59 am
Drill Attachment for Brushing out Slide
Dana Hofer uses a manual brush for such a thing. (Check out his "professional trombone slide servicing" photo album in this link: http://www.danahoferbrassrepair.com/photo_gallery.htm#slide)
I'm pretty sure that long brush could be modified for use in a drill. However, you could only use a drill if the rod were still enough and if it weren't badly warped.
I'm pretty sure that long brush could be modified for use in a drill. However, you could only use a drill if the rod were still enough and if it weren't badly warped.
-
- Posts: 0
- Joined: Sat Mar 31, 2018 11:59 am
Drill Attachment for Brushing out Slide
My repair guy has one of these. Just an old motor turning slow with a cleaning rod.
I have noticed that every time he uses it he also re-aligns the slide.
I have noticed that every time he uses it he also re-aligns the slide.
-
- Posts: 0
- Joined: Sat Mar 31, 2018 11:58 am
Drill Attachment for Brushing out Slide
Quote from: Bruce the budgie on Jul 01, 2017, 08:08AMThe fellow who recently smoothed out a couple of dents in my bell stem told me about a bench-mounted motor he uses for slide tube treatment, with a pedal to control the speed.
The guy who did my 2B has the same - a lathe, with a slide cleaning rod attached. He changed the cleaning/polishing bit at the end a few times, and left the interior of the outer slide very good. Then he spent a good hour fine-tuning it. Variable speed lathe, constantly changing the polishing cloth, lots of practice.
The guy who did my 2B has the same - a lathe, with a slide cleaning rod attached. He changed the cleaning/polishing bit at the end a few times, and left the interior of the outer slide very good. Then he spent a good hour fine-tuning it. Variable speed lathe, constantly changing the polishing cloth, lots of practice.
-
- Posts: 0
- Joined: Sat Mar 31, 2018 11:58 am
Drill Attachment for Brushing out Slide
Quote from: Bruce the budgie on Jul 01, 2017, 08:08AMThe fellow who recently smoothed out a couple of dents in my bell stem told me about a bench-mounted motor he uses for slide tube treatment, with a pedal to control the speed.
The guy who did my 2B has the same - a lathe, with a slide cleaning rod attached. He changed the cleaning/polishing bit at the end a few times, and left the interior of the outer slide very good. Then he spent a good hour fine-tuning it. Variable speed lathe, constantly changing the polishing cloth, lots of practice.
The guy who did my 2B has the same - a lathe, with a slide cleaning rod attached. He changed the cleaning/polishing bit at the end a few times, and left the interior of the outer slide very good. Then he spent a good hour fine-tuning it. Variable speed lathe, constantly changing the polishing cloth, lots of practice.